-
SpotlightThe power of movement
October 2024
The complex cross-border supply chain powering your drive
Global trade is changing, with businesses looking to balance opportunities in high-growth markets with resilience and stability. In this rapidly-evolving landscape, innovative and dynamic finance solutions are crucial to unlock capital and direct it to where it’s needed most.
Producing impactful technology – such as electric vehicles – can involve numerous companies across multiple markets. From obtaining and processing raw materials, to shipping parts and components across borders, these complex supply chains require financing at every stage.
Connector banks which combine global scale with local expertise can make these supply chains more robust. Take electric vehicles. Creating the battery for an electric car or truck means connecting businesses around the world, from Australia to Sweden. At Standard Chartered, we provide financial services at every step.
We don’t just help our clients unlock opportunities in different places. We also help them to join up the different stages of a global journey which turns lithium into batteries, batteries into horsepower, and – one day – back into the supply chain through recycling.
Before an electric vehicle hits the road, its battery has already gone on a journey. This is the story of that journey – and what it tells us about finance in a changing world.
Upstream
On a road in Shenzhen, taxis with green number plates hurry to collect customers. In a parking space in Hamburg, a family plugs in their car to charge for the night. In Surat, electric buses pause by the roadside to pick up passengers.
From behind the wheel of today’s modern electric vehicles (EVs), it’s easy to forget that one of the key components is often sourced from an unlikely place: a hole in the ground in Western Australia.
To some, the setting may sound unremarkable. But the element excavated here – lithium – is set to play a key role in powering the vast fleet of EVs needed in the decades to come.
10x
The amount the lithium sector must increase in size between 2020 and 2035 to meet projected supply needs.
Already used in laptops and phones, lithium’s light weight and high energy density make it perfect for creating the high-performing batteries crucial to this new generation of vehicles.
But the mass adoption of EVs, which some hope will reduce transport emissions, doesn’t just require an increase in lithium supply. It also needs a robust supply chain to turn minerals from one location into a battery supply pack which can power cars around the world.
Today, over 50 per cent of the world’s lithium supply is dug up as a mineral called spodumene from open-cast mines in Australia.
In terms of reserves, Australia is second only to Chile, where lithium ore is slowly evaporated from groundwater in vast, shallow pools.
An average EV battery pack needs eight kilos of lithium and exploration of further deposits is proceeding at pace to match production demand.

This demand isn’t linear: recent weakness in the Chinese economy, where most EVs are manufactured, has contributed to a slump in lithium spot prices. But this recent pullback doesn’t negate the need for longer-term growth.
“From 2020 to 2035, the lithium sector has to grow by over 10 times,” says Richard Horrocks-Taylor, Global Head of Metals and Mining at Standard Chartered. “That’s a real mountain to climb for an industry which often takes a long time to develop projects.”
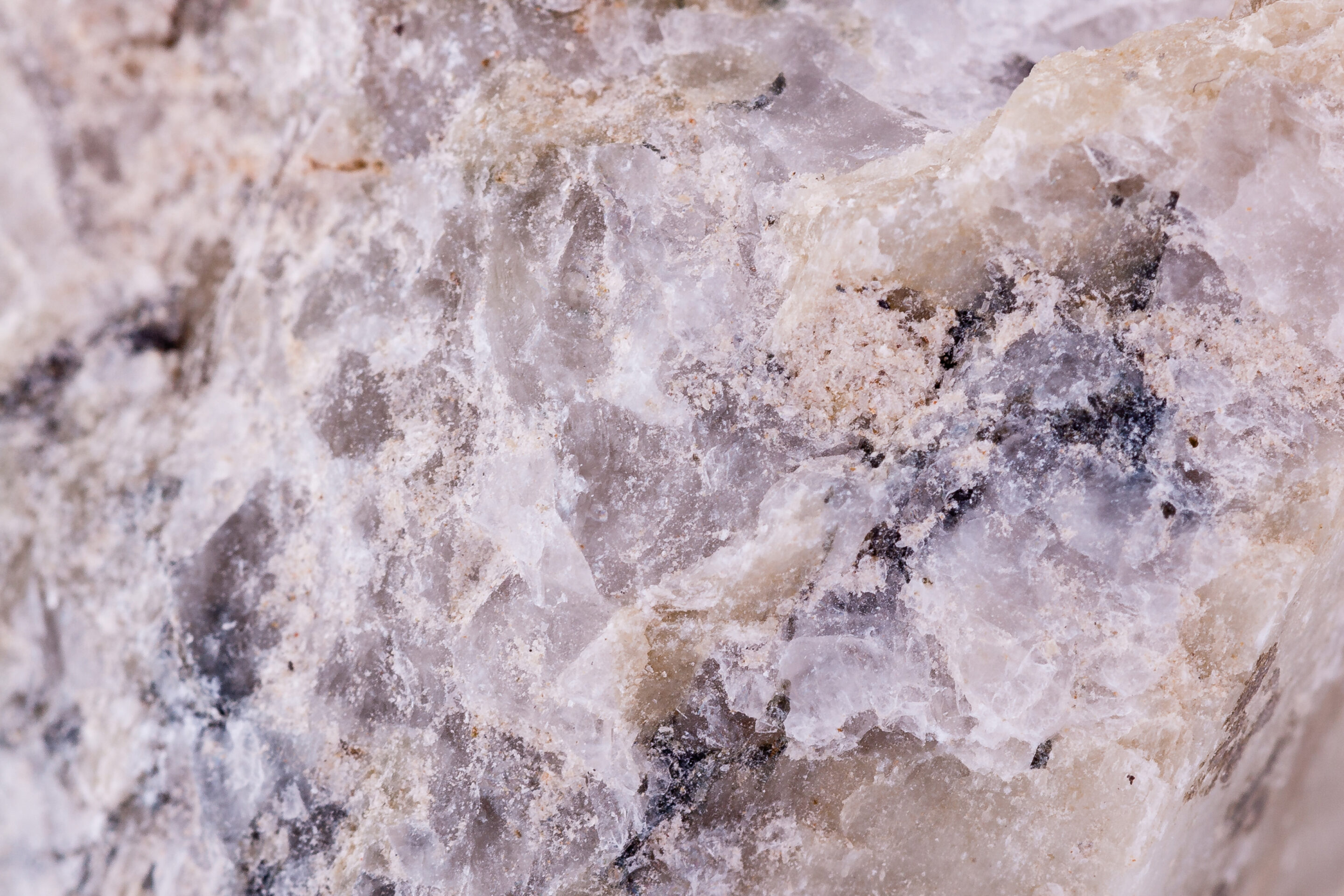
Mainstream
Spodumene is striking to look at: crystalline and often tinged with streaks of pink, yellow and purple. But as a hard rock, it doesn’t have much practical use.
A complex, energy-intensive series of chemical processes are needed to draw out the pure lithium it contains.
Most of these processes happen in China, home to over 60 per cent of the world’s refining capacity.
There’s a big opportunity to match capital to the right assets.
Richard Horrocks-Taylor
Global Head of Metals and Mining
China also has a significant position in the next stage of the process.
After it’s extracted, lithium is transformed into thin wafers and combined with other materials, such as copper, manganese or nickel, to make the cathodes that are fitted into each EV battery cell.
Downstream
Each battery pack has hundreds of these individual cells sandwiched together. Today, much of this activity also takes place in China.
But new battery ‘gigafactories’ are cropping up in many new locations, from Buffalo, New York to Brandenburg, Germany.
“There’s a big opportunity to match capital to the right assets,” Horrocks-Taylor says, “both upstream and with these types of downstream processing facilities.”
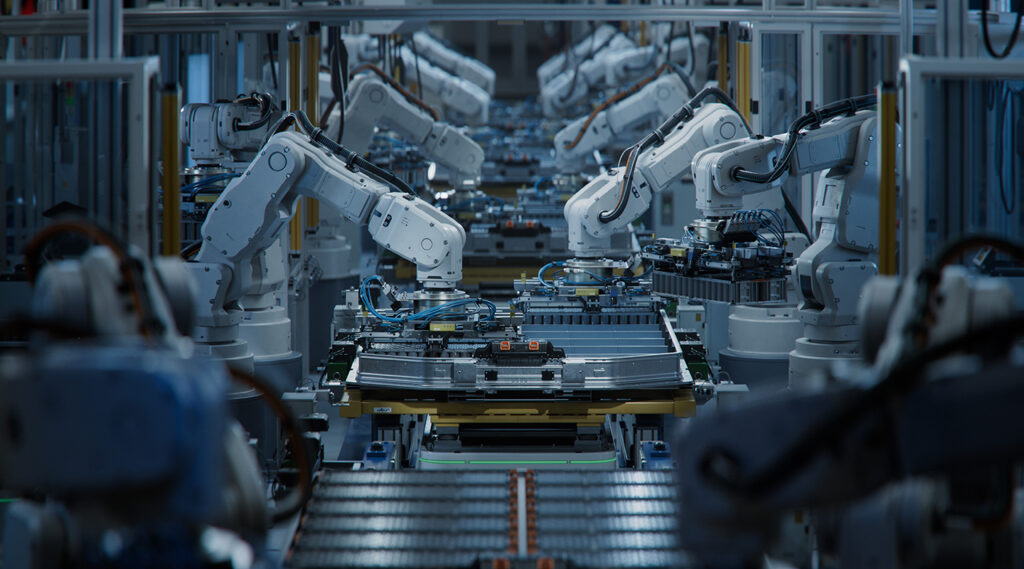
This will diversify a critical section of the supply chain, but also mean that the components, and finished batteries, will need to be transported between different markets.
What’s more, new gigafactories can be a great distance from automobile production lines, where the batteries are fitted to new EVs and then shipped to customers across the world. In this case, trade finance becomes critical.
“We believe some of the more sophisticated groups will be looking at these supply chains again,” says Horrocks-Taylor. That could include backward integration where companies buy or merge with suppliers earlier in the chain, helping them gain control of the materials and processes which they need to deliver batteries.
Second life
Even after cars have been shipped to customers, the lithium journey is not complete. Lithium-ion batteries can be depleted and recharged thousands of times without losing significant capacity, making them ideal for delivering reliable vehicle range.
But their lifespan is not infinite. Most are expected to fall below EV performance standards within 10 years.
Yet they can still be put to good use. For example, by combining thousands of ex-EV batteries, it’s possible to create large-scale grid storage solutions, which have lower performance demands.
These store energy to be released into a power grid as it’s needed and can provide a reliable source to complement more intermittent renewable energy installations.
Research estimates this so-called ‘second life’ supply could hit 200 gigawatt-hours per year by 2030.
“We’re now involved in transactions right the way through that value chain, including end-of-life recycling,” says Ben Daly, Global Head of Transition Finance at Standard Chartered.
200 GWh
The estimated yearly output that ‘second life’ supply could hit by 2030.
Old batteries can also be directly recycled by breaking open the packs, extracting the valuable metals within, and placing them back into the supply chain. This can help meet demand while reducing dependence on mining.
However, this type of recycling is an energy-intensive process, and a relatively new venture for many firms. Boosting this ‘circular economy’ therefore requires significant investment to improve efficiency and cost-effectiveness.
“The challenge of mining’s disruptive nature is well-known – although there are tools we use to help manage this, including those offered by industry bodies such as the International Council on Mining and Metals,” says Claire Orton, Global Head of Environment and Social Risk Management at Standard Chartered.
“As the world continues to respond to demand for critical minerals, there is a need to think carefully about the trade-offs, and seek to limit any negative impact on people, communities and the environment as much as possible.”
“Whilst there is no silver bullet for the energy transition,” says Daly, “batteries – whether in EVs or storage – have a big role to play and require investment.”
Further, to achieve the scaling required, having robust and efficient supply chains will be critical.
The story of a lithium-ion battery reminds us that technology with the potential to be part of the transition picture – whether EVs or battery recycling – relies on multiple companies coming together in one cross-border supply chain.
Only with the right financing, in the right places, can these connections be made – from extraction, to processing, to the assembly line and, ultimately, to roads and grids around the world.
Funding every step of the journey
Case Study
Supporting energy storage in Australia with Rangebank
Case Study
Next stop, electric buses with GreenCell Mobility in India
Case Study