COVID-19: reshaping the future of supply chains
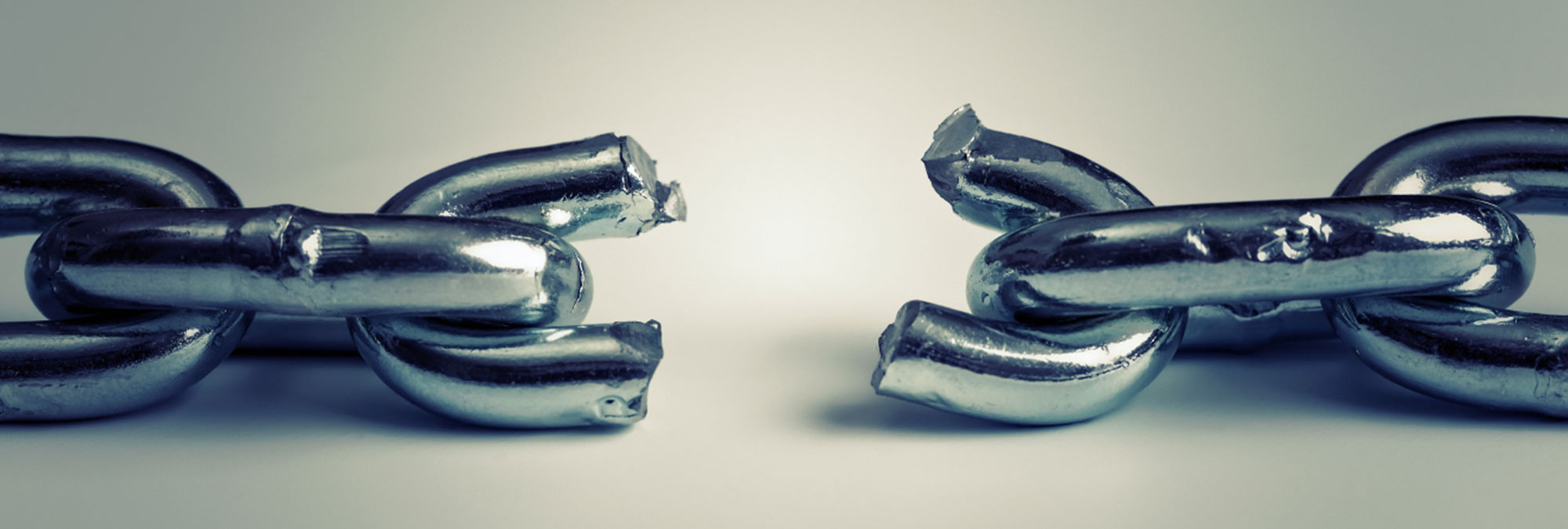
Will emerging markets lose advantage? Will China’s dominance end? Will protectionism become the new normal?
These are some of the many questions cropping up, as the coronavirus upends global business operations.
The pandemic has exposed many weaknesses in the current structure of global supply chains. Advantages such as cheap labour, lower transportation costs, communications technology and reduced tariff barriers gave rise to global supply chains (GSC). They are now being blunted by disruptive technology and a changing geopolitical landscape, dominated by wealth inequality and protectionist narratives.
A supply chain that is dependent on a single source is vulnerable to paralysis when that source gets cut off – that’s concentration risk, which COVID-19 has made the dominant focus for businesses.In response, companies may accelerate efforts to re-shore or near-shore production, with inventories shifting away from highly efficient but vulnerable (just-in-time) to more capital intensive (just-in-case) processes.
Consider car manufacturing: it takes 2,500 components to make a car, but just one component to not make a car. The impact of disruption is already visible in the UK car manufacturing, which operated on the assumption of frictionless intra-European trade, with parts sourced from four to five different markets.
The pitfalls of over-reliance on a region were evident when the Hubei province in China shut down, disrupting the supply chains of 300 of the world’s top 500 companies, who have facilities there.
The advancement of robotics and automation has enabled high-cost destinations to bring low-skilled manufacturing back onshore from low-cost offshore centres. This technology-driven ‘reshoring’ or ‘inshoring’ of manufacturing has the significant advantage of reducing the time from design to delivery. This enables wealthier demand destinations to better control their supply chains, particularly of concern now for essential products such as medical supplies.
Change is already underway – in its April 2020 annual Reshoring Index, consulting firm Kearney cited a “dramatic reversal” of US manufacturer sourcing from Asia to domestic suppliers in 2019, most likely driven by the US-China trade war.
Some US tech companies, for instance, have already started to move manufacturing out of China, while some carmakers said they were considering modifying their supply chains in the light of the US-China trade war.
GSCs are highly dependent on the success of globalisation and COVID-19 is accentuating the pre-existing ambivalence towards globalisation at a time when multilateralism is needed more than ever to coordinate the response (medical, political and economic).
In addition, the US, the chief architect of a global world order, has been engaging in global trade as a zero-sum game with Trump at the helm, dealing a huge blow to the case for globalisation.
This does not mean that globalisation has stopped, but rather that it could be reshaped. Within this, the EU is a key source of support for globalisation and the preservation of an international rules-based order based on multilateral cooperation.
In this geopolitical context, regional trade has become more prominent, particularly in Asia. With China metamorphosising from the world’s low-cost manufacturing hub to a final demand destination, more of the goods manufactured via Asia’s supply chains have remained in Asia. Developing Asia has cemented its position as a dominant regional trade hub, buoyed by demand from China, first as part of its supply chain, and increasingly to cater to its final demand.
While global trade and the structure of GSCs, in particular, has evolved since the GFC, we expect a few changes to become more evident over time.
China has shares of over 50 per cent in several manufacturing supply chains so companies and governments focussing on reducing the dominance of any country in supply chains, might mean a smaller role for China. However, China’s dominance of world trade is unlikely to be challenged in the near future. In fact, China’s growing importance as a source of foreign direct investment (FDI) for other emerging markets (for example via the Belt and Road Initiative) is also likely to help maintain its position as a mega-trader.
In addition, while the shift towards regional supply chains is becoming clearer, factory relocation tends to be a multi-year project involving long planning times and heavy investment; the current macro backdrop is probably not conducive to making such commitments.
This is evident from our proprietary survey of firms in the Pearl River Delta: among two-thirds of respondents (250 manufacturers) that were considering, or planned to actively consider, moving overseas, most (56 per cent) remained in the ‘still under consideration’ phase.
While COVID-19 is catalysing the acceleration of many existing trends, there remains a strong case for the future of trade between markets – the shape of the new world trade order will emerge once the pandemic passes.
To read the full report, subscribe to our Global Research portal.