Transforming operations to succeed in a post-COVID-19 world
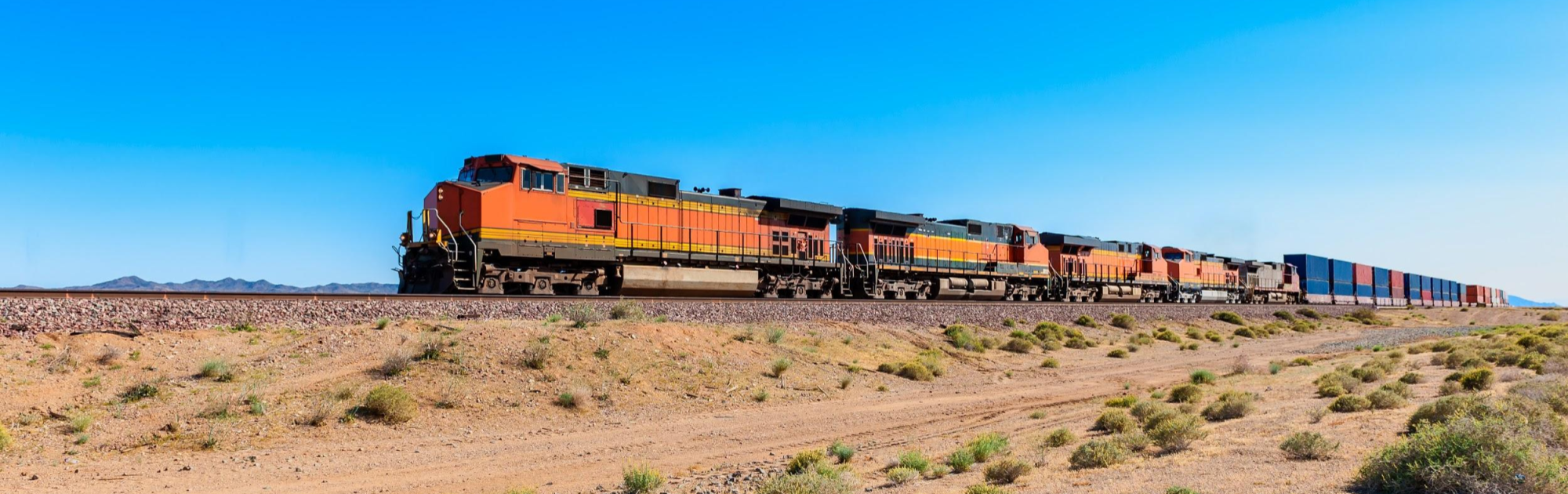
We live in a hyper-connected world with complex and expanding supply chains. However, recent geopolitical and trade tensions coupled with the onset of COVID-19 have accelerated the fundamental shifts in these global linkages. Therefore, as companies progress along the ‘Preservation and Stability’ stage (i.e. Stage 2) on the ‘Road to Resilient Growth’, efforts in building agility and transparency in operations and across supply chains become increasingly important. This requires mid-corporates to have a clear view across the value chain – both upstream and downstream – to accurately assess their ability to meet projected customer demand as well as predict any upcoming bottlenecks or challenges such as shortages in raw material supplies. They also need to be agile, able to quickly respond and adapt to spikes in demand or overcome any issues in supply, production and / or distribution to still meet customer expectations.Based on our survey1, the top concern for mid corporates as they embark on reinstating operations is uncertainty related to end-consumer demand (61 per cent), followed by growing pricing pressures (53 per cent) and rising cost of materials (50 per cent). In order to effectively address these challenges, mid-corporates need to undertake initiatives across the value chain and recalibrate their operational strategy to deliver a differentiated customer experience.
Traditionally, mid-corporates have pursued strategies focused on profitable growth, with cost reduction and revenue enhancement being key priorities. As such, they have often adopted the ‘just-in-time’2 approach to production, where exact quantities of material are supplied to each part of the production process only when needed. In a relatively stable environment, organisations can rely on this approach to reduce costs and boost profitability. However, increasing disruption renders these organisations highly vulnerable to sudden and unpredictable changes in supply or demand.
With the scale of disruption wrought by the pandemic, a strategic shift away from a ‘just-in-time’ to a ‘just-in-case’2 approach is necessary to achieve resilient growth. The just-in-case approach builds in the necessary redundancy with buffer stocks held at every stage in the production process, helping mid-corporates absorb the shock generated by unforeseeable scenarios and contingencies. With 60 per cent of the mid-corporates surveyed considering developing alternative sourcing options and establishing flexible production capabilities, the ‘just-in-case’ approach has clearly gained traction.
Some common tactics mid-corporates are employing to tackle ongoing challenges include short term measures to build in buffers (or, ‘elements of redundancy’) across various operational areas, such as holding larger inventory of critical raw materials, growing local / regional sourcing and stocking up high demand products. In the medium term, this would be followed by greater adoption of technology for operations to become more efficient, paving the way for more profitable and resilient growth in the longer term.
Mid-corporates need to consider taking these three actions to transform their operational processes as they tackle supply chain and operational disruptions:
The current pandemic has caused significant disruptions across the supply chain, resulting in procurement delays and shortages in critical raw materials. Improving transparency and diversifying sources within the supplier network is therefore essential as organisations look to resume production. Companies can employ the following to improve their procurement processes and build resilience into their supplier network
Operational hazards faced during the peak of the COVID-19 crisis such as production stoppages, delayed shipments, tightened liquidity, uncertain demand and inventory shortages have brought to light the importance of establishing practices that minimise operational risks. For example, while keeping a lean inventory management system minimises overall costs, it exposes companies to greater risk of losing sales and revenue during volatile times. Instead, maintaining strategic inventory buffers would allow companies to meet customer expectations regardless of potential demand spikes or supply issues. As mid-corporates strive towards recalibrating and optimising manufacturing operations, they need to consider adopting the following measures:
The third action requires enhancing distribution capabilities to deliver high ‘On-Time and In-Full’ (OTIF) performance in an efficient manner, while protecting against possible disruptions. Below are some tactics mid-corporates can consider to foster resilient distribution processes:
As mid-corporates progress along the ‘Road to Resilient Growth’ and enter Stage 3 (‘Preparing for Growth’), operational agility will become a strategic differentiator for mid-corporates. It entails not just diversification but spans the entire value chain, nurturing a corporate culture of resilience, transparency and a more integrated technological adaptability. Reliability will also play a central role in defining buyer-supplier relationships going forward.
The next point-of-view in our series will explore new ways of working and will offer insights into managing, motivating and retaining a high performing workforce with a clear sense of purpose, as mid-corporates move along their journey towards resilient growth.
[1] Survey commissioned by Standard Chartered in June 2020 and completed by 205 mid-corporates (annual revenue USD100m-500m) based in Mainland China, Hong Kong, Singapore, Malaysia and India.
2 Just-in-time practices are aimed at the total elimination of waste, to minimise the costs of holding stocks of raw materials, work-in-progress and finished goods by supplying to each part of the production process exactly what is needed, when it is needed and in the quantity it is needed. On the other hand, the just-in-case system has buffer stocks held at every stage in the production process ‘just in case’ there is a production problem or demand rises unexpectedly.
3 Cross-docking refers to transfer points where inbound product flow is synchronised with outbound product flow, usually with the assistance of third-party logistics companies (3PLs), to essentially eliminate storage of inventory. It helps in significant cost reductions and reduced lead times as products can be stored in a warehouse and additional 3PL services can be performed without a long-term storage commitment.
Watch now
[iframe title=”Video” width=”800″ height=”450″ scrolling=”no” marginheight=”0″ marginwidth=”0″ src=”https://www.youtube.com/embed/https://www.youtube.com/watch?v=_OLHSCK7S5A?showinfo=0&rel=0″]
PwC, ‘COVID-19 How PwC can help you maintain Financial & Operational stability’
PwC, ‘Connected and autonomous supply chain ecosystems 2025’
PwC, ‘COVID19 Operations Strategic Response – Path to Recovery and Resilience’, March 2020
Standard Chartered, ‘COVID-19: reshaping the future of supply chains’, May 2020
Standard Chartered, ‘From just in time to just in case: COVID-19 brings supply chain resilience to the fore’, April 2020
Standard Chartered, ‘Supply chain lessons from COVID-19’, March 2020
Harvard Business Review, ‘Coronavirus Is a Wake-Up Call for Supply Chain Management’, March 2020
CSCMP’s Supply Chain, ‘Preparing warehousing and distribution for a frontline role by 2030’, July 2020
This material has been prepared by PricewaterhouseCoopers Consulting (Singapore) Pte Ltd. (“PwC”) at the request of Standard Chartered PLC and its affiliates (“SC Group”) in accordance with the agreement between PwC and SC Group. Other than to SC Group, PwC will not assume any duty of care to any third party for any consequence of acting or refraining to act, in reliance on the information contained in this report or for any decision based on it. PwC accepts no responsibility or liability for any use of this report by any third party, including any partial reproduction or extraction of this content.